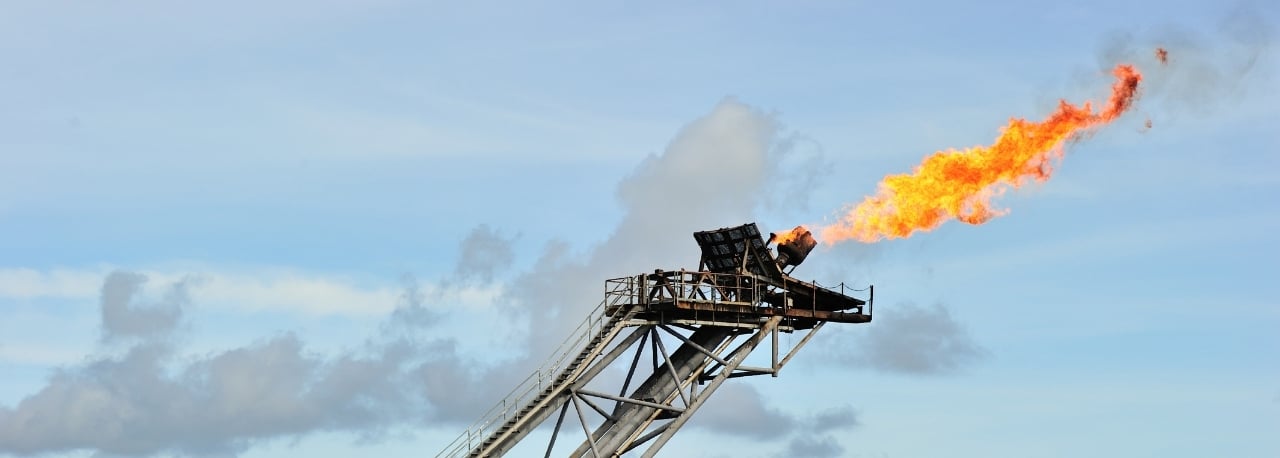
Service:
Flare Assessment
Facility:
FPU / FPSO
Elimination of a Remote Flare System
An offshore floating production facility operated with two flare systems: one on a boom riser and another remotely located. The remote flare required substantial gas to operate, driving up costs and emissions. The offshore facility sought to consolidate both flares into the boom riser system to reduce operational expenses and improve efficiency, however concerns arose regarding feasibility, thermal radiation impacts, and increased backpressures on relief devices.
Our Solution
Smith & Burgess performed a detailed flare system analysis using individual relief system design data. By consolidating the relief and depressuring loads into site-wide failure contingencies, our engineers identified peak flare system loads and established pressure design criteria. Collaborating closely with flare vendors, we identified a dual-flare tip solution that integrated high-pressure and low-pressure flare tips onto the existing boom riser. This approach eliminated the need for the remote flare while maintaining system reliability and safety. Through expert analysis and collaboration, we provided a solution that met operational, safety, and financial goals, showcasing our commitment to delivering tailored, high-impact results for complex engineering challenges.
Results
- Cost Savings: The new design was implemented at under $500,000–less than 10% of the site's initial conceptual estimate.
- Enhanced Efficiency: Reduced capital expenditures and ongoing operational costs.
- Minimized Downtime: Facility upgrade impact was shortened from weeks to days.
- Improved Safety: The consolidated system enhanced overall facility safety by streamlining flare operations.
- Lower Emissions: Achieved a significant reduction in operational emissions and maintenance costs.