Relief & Flare Studies
Relief and flare systems are critical safety components that protect industrial operations from overpressure events, equipment failure, and hazardous releases. Smith & Burgess provides comprehensive Relief & Flare Studies to help facilities comply with OSHA’s Process Safety Management (PSM) standard [29 CFR 1910.119(d)] and the EPA’s Risk Management Program [40 CFR 68], while ensuring optimal system performance.
Our experienced engineers ensure that your relief systems are properly designed, documented, and maintained–safeguarding your people, assets, and the environment.
Why Relief & Flare Studies Matter
Facility Changes Demand Updated Analyses
Many facilities have undergone expansions or operational changes since their original relief systems were installed—often without updating system design accordingly. This creates serious safety and compliance gaps.
Smith & Burgess provides engineering assessments to identify and mitigate these risks. Our engineers optimize relief and flare system designs with minimal physical modifications, ensuring discharge locations meet facility siting and PSM requirements.
Customized Relief and Flare Studies
Each facility has unique challenges, from varying process conditions to complex materials and flow dynamics. Our team works directly with you to understand these parameters and develop customized solutions that exceed compliance requirements.
We also help facilities reduce emissions to meet the applicable regulatory standards, including [40 CFR 60 Subpart JA].
Flare System Optimization
Using advanced modeling tools and engineering analysis, our flare studies evaluate header hydraulics, flare stack design, and gas composition. Our approach ensures that mitigations are effective, emissions are minimized, and capital costs are contained.
Whether updating an aging system or designing for future flexibility, Smith & Burgess delivers practical, risk-based recommendations aligned with best practices and RAGAGEP.
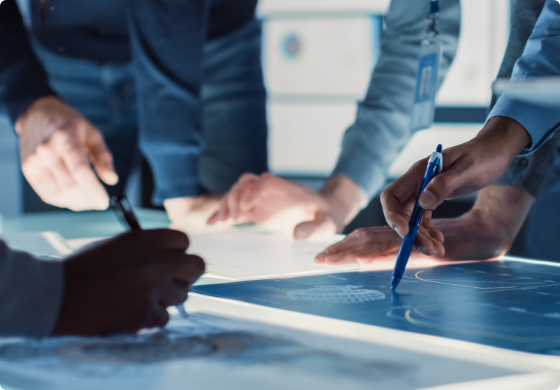
Relief System Analysis
Our relief system analyses cover everything from relief valve sizing to system interaction and overpressure scenarios. We ensure:
- Accurate relief device sizing
- Proper documentation per PSI and corporate standards
- Adherence to OSHA PSM [29 CFR 1910.119(d)] and EPA RMP [40 CFR 68] requirements
Our engineers apply decades of experience and leading engineering practices to evaluate and validate the performance of each relief device within the context of your facility’s unique operating conditions.
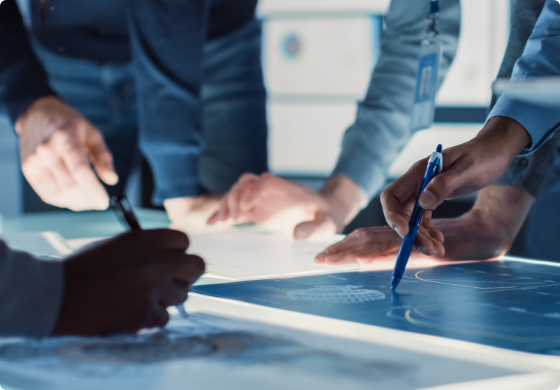
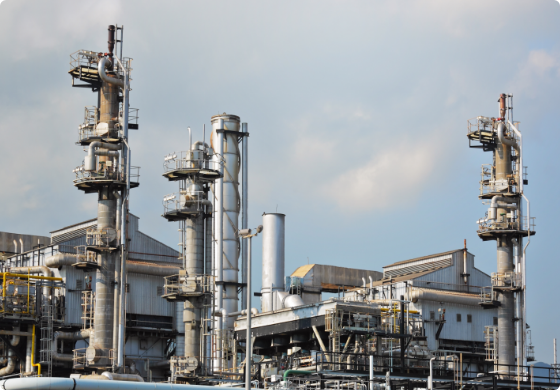
Flare System Analysis
Flare systems must do more than meet design capacity—they must align with operational flexibility, maintenance strategies, and environmental goals. Our analysis includes:
- Header and lateral piping analysis
- Knockout drum and seal drum evaluations
- Flare stack capacity and dispersion modeling
- Emissions reduction and compliance planning
We identify design inefficiencies, operational bottlenecks, and environmental gaps to ensure your flare system operates safely and cost-effectively.
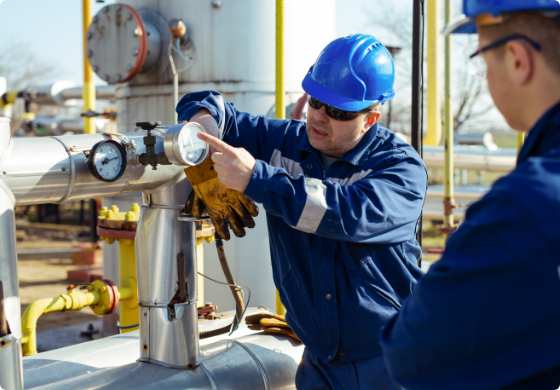
Concern Mitigation Planning
Relief and flare system assessments often identify noncompliance with RAGAGEP. Smith & Burgess helps you bridge these gaps through actionable, cost-conscious mitigation planning. We prioritize recommendations that:
- Enhance process safety
- Minimize operational disruption
- Optimize budget and resources
We balance best practice adoption with real-world constraints to help you achieve your safety and compliance goals.
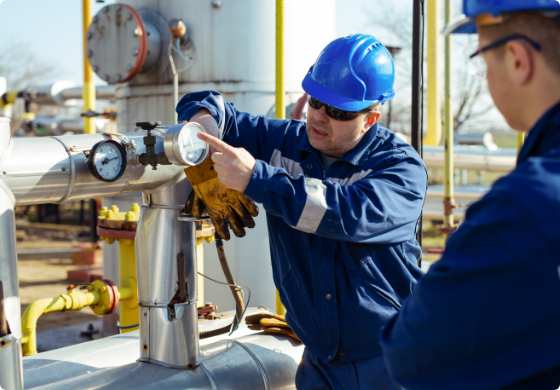
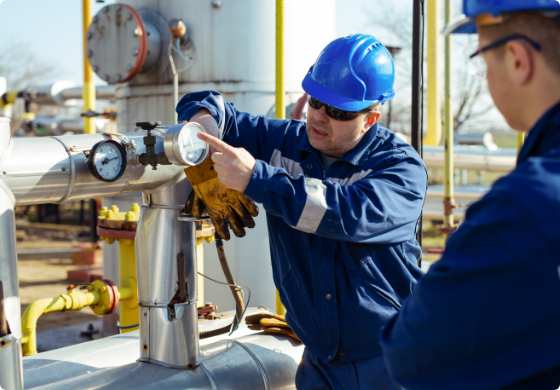
SalusTM by Smith & Burgess
Need to maintain your PSI evergreen program with ease? Salus is our proprietary software designed to streamline relief system data management and compliance. With intuitive dashboards, real-time updates, and integration with your facility’s existing systems, Salus helps ensure your relief and flare documentation stays accurate and audit-ready.
Guidelines and Standards Development
Navigating technical standards can be complex and time-consuming. Smith & Burgess helps industrial facilities interpret the latest industry guidelines into clear, facility-specific procedures that align with Recognized and Generally Accepted Good Engineering Practices (RAGAGEP), as required by OSHA [29 CFR 1910.119] and the EPA Risk Management Program [40 CFR 68].
We translate high-level regulatory standards into practical, implementable solutions tailored to each facility. Our engineers actively participate in the industry committees that shape these guidelines—American Petroleum Institute (API), Energy Institute (EI), and the American Society of Mechanical Engineers (ASME)—ensuring your facility benefits from the most current, authoritative recommendations in relief system design, flare capacity and performance, environmental compliance, and documentation best practices.
Why Choose Smith & Burgess?
GLOBAL EXPERTISE
We support major industrial facilities worldwide with proven strategies tailored to local and global standards.
COMPREHENSIVE SUPPORT
From PSI gap assessments to evergreen programs, we provide end-to-end support.
CUSTOMIZATION
Our engineering recommendations are tailored to each facility’s evolving needs and compliance requirements.
INDUSTRY LEADERSHIP
Our active involvement in API and ASME committees keeps us ahead of regulatory changes and best practices.